Theoretical modal models found their practical relevance as early as the 1900s, particularly in the field of aeronautical development. Pioneering commercial airplane manufacturers such as the Wright Company, Short Brothers, Glenn Curtiss, and others relied heavily on theoretical and empirical calculations to gain sufficient confidence to achieve flight-worthy designs. Academia and universities played a vital role in supporting this emerging industry, contributing foundational research and expertise.
These early calculations were largely effective due to the relatively simple nature of the aircraft at the time - limited in size, speed, and complexity of dynamic loads. The modal boundary conditions that engineers considered were constrained, leading to simplified matrix models and outcome predictions.
Typical modal stabilisation curve
At its core, the term modal refers to the shape that a structure assumes at specific natural frequencies. When a physical object is excited with sufficient force, it responds with vibration -this dynamic behavior can be measured and analyzed. Key modal parameters include the natural frequencies, corresponding mode shapes (deflection patterns), and damping characteristics. Collectively, these are referred to as modal quantities or eigenvalues.
Until the late 1940s, theoretical methods - often involving multiple assumptions - were the primary means of modal analysis. Gradually, experimental modal testing began to gain ground, thanks to the advent of instrumentation and basic data acquisition systems. With the rise of computational capabilities and early software tools, the accuracy and confidence in physical modal testing significantly improved. As a result, modal data became essential for both the pre-qualification and post-validation stages of design, particularly in aerospace and automotive industries.
The modal parameters—frequency, mode shape, and damping—together form the dynamic signature of any structure under test. Frequencies identify critical operating zones, mode shapes describe physical motion patterns, and damping values reveal energy absorption characteristics.
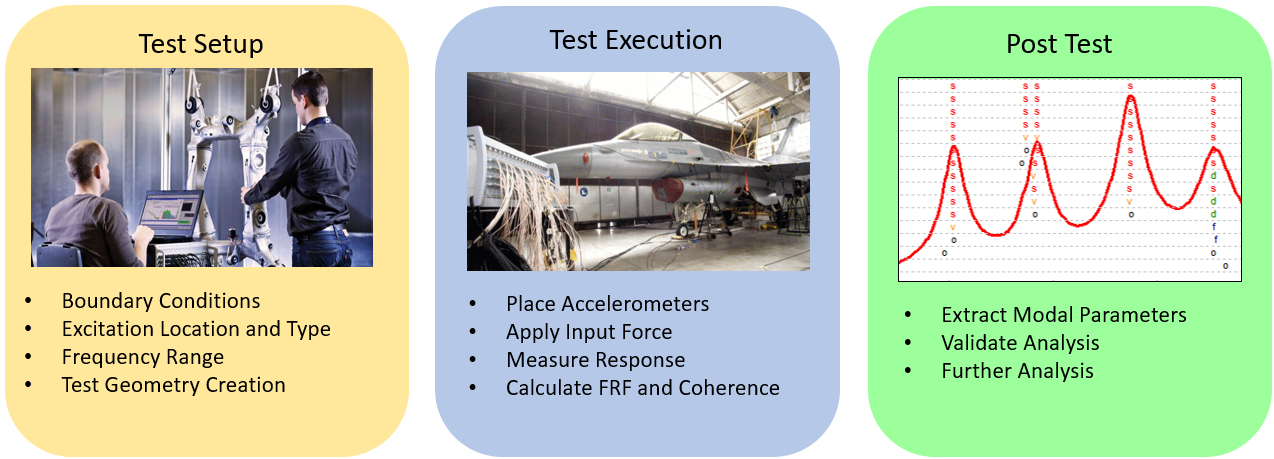
Going beyond basic testing, modal sensitivity analysis and modal modification predictions offer powerful tools for design refinement. These computations assist engineers in optimizing mass and stiffness distributions, ultimately leading to dynamically stable designs. When combined with high-quality finite element (FE) solvers, the integration of test and simulation data brings substantial value to the entire design process.
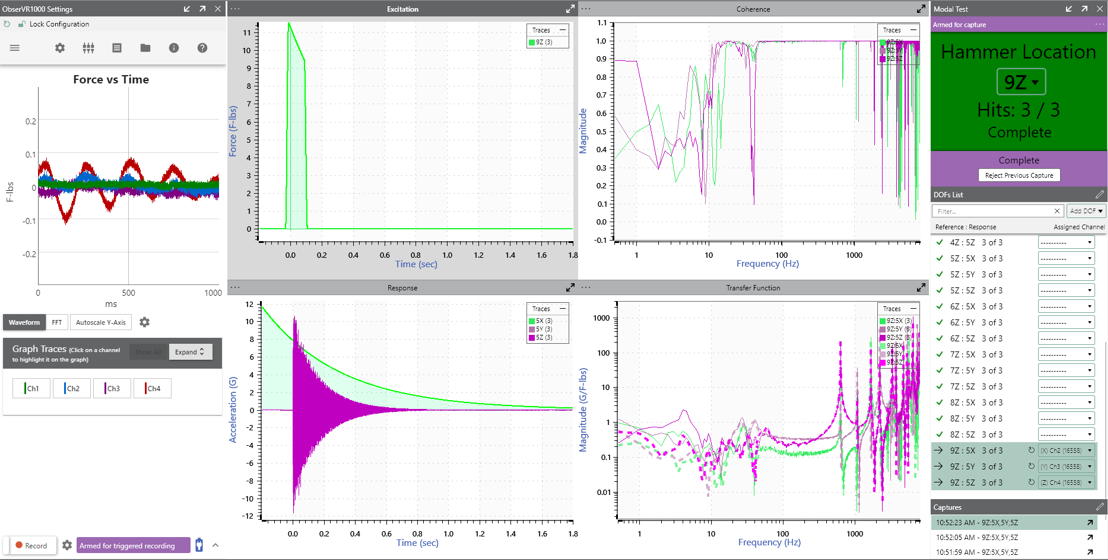
Various parameters observed during a Modal testing
What was once a proprietary validation methodology reserved for aerospace, defense, and automotive applications has now permeated many other industries. Modal testing is increasingly recognized for its relevance in addressing structural dynamics across a wide range of sectors.
Modern modal analysis benefits from advanced software ecosystems that tightly integrate testing, analysis and model updating workflows. Techniques such as poly-reference methods and robust Modal Assurance Criterion (MAC) matrix algorithms ensure repeatable, reliable results across extensive test programs.
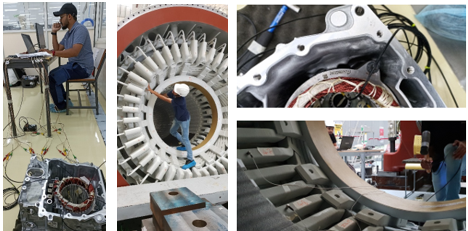
Modal testing conducted by our team on 660MW generator and Engine Integral body part
At NV Dynamics, we employ industry-leading SIEMENS Test.Lab software in conjunction with SIEMENS Scadas XS hardware. This unified platform allows for seamless acquisition and analysis. It has enabled us to execute complex modal testing projects - including the 660MW generator of GE, where we validated FE modal responses from end windings and a new engine case development initiative in collaboration with Toyota Motor Corporation.